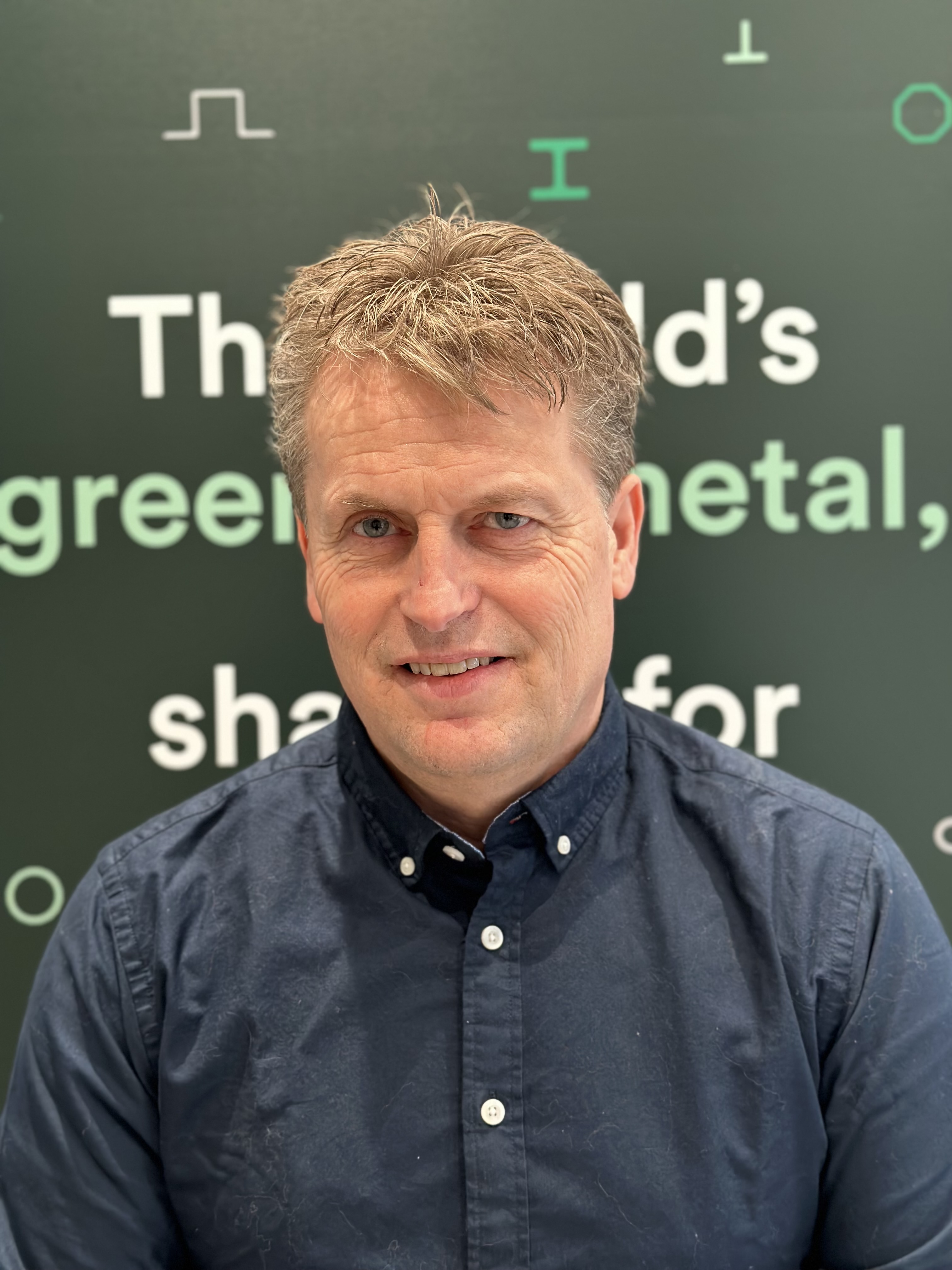
Svein Inge Nerland
Salgssjef
Understanding Dies in Aluminum Extrusion
Typically, extrusion dies are made from H13 tool steel due to its high tolerance to pressure, heat, and wear. The die's design is complex and involves computer-aided design (CAD) software to ensure precise measurements. The die must be designed to consider factors like aluminum alloy properties, desired shape, thickness, and post-extrusion processing.
Solid Dies: Most basic type, used for solid shapes like rods and beams.
Hollow Dies: More complex, for hollow sections. They include "bridges" or "webs" that allow aluminum to flow around them, creating hollow sections.
Semi-Hollow Dies: For profiles that are almost hollow but have a partially enclosed void.
Die life can vary based on several factors including the complexity of the profile, the aluminum alloy used, and the extrusion conditions. Regular maintenance includes polishing and cleaning to remove any aluminum buildup. In some cases, dies can be refurbished to extend their life.
During extrusion, the aluminum billet is heated and pressed against the die by the extrusion press. As the aluminum flows through the die opening, it takes on the cross-sectional shape of the die, emerging as an elongated piece with the desired profile. This piece is cooled, straightened, and cut to length.
Advancements in die technology continue to push the boundaries of what can be achieved through aluminum extrusion. Computer simulation of the extrusion process, for example, allows for precise predictions of how the aluminum will flow through the die, leading to more efficient designs and reducing the time needed to bring new profiles to market.
Dies are at the heart of aluminum extrusion, translating design creativity into tangible products. Their importance cannot be overstated, as they directly influence the efficiency of production, the quality of the extruded profiles, and the scope of applications for the aluminum products.