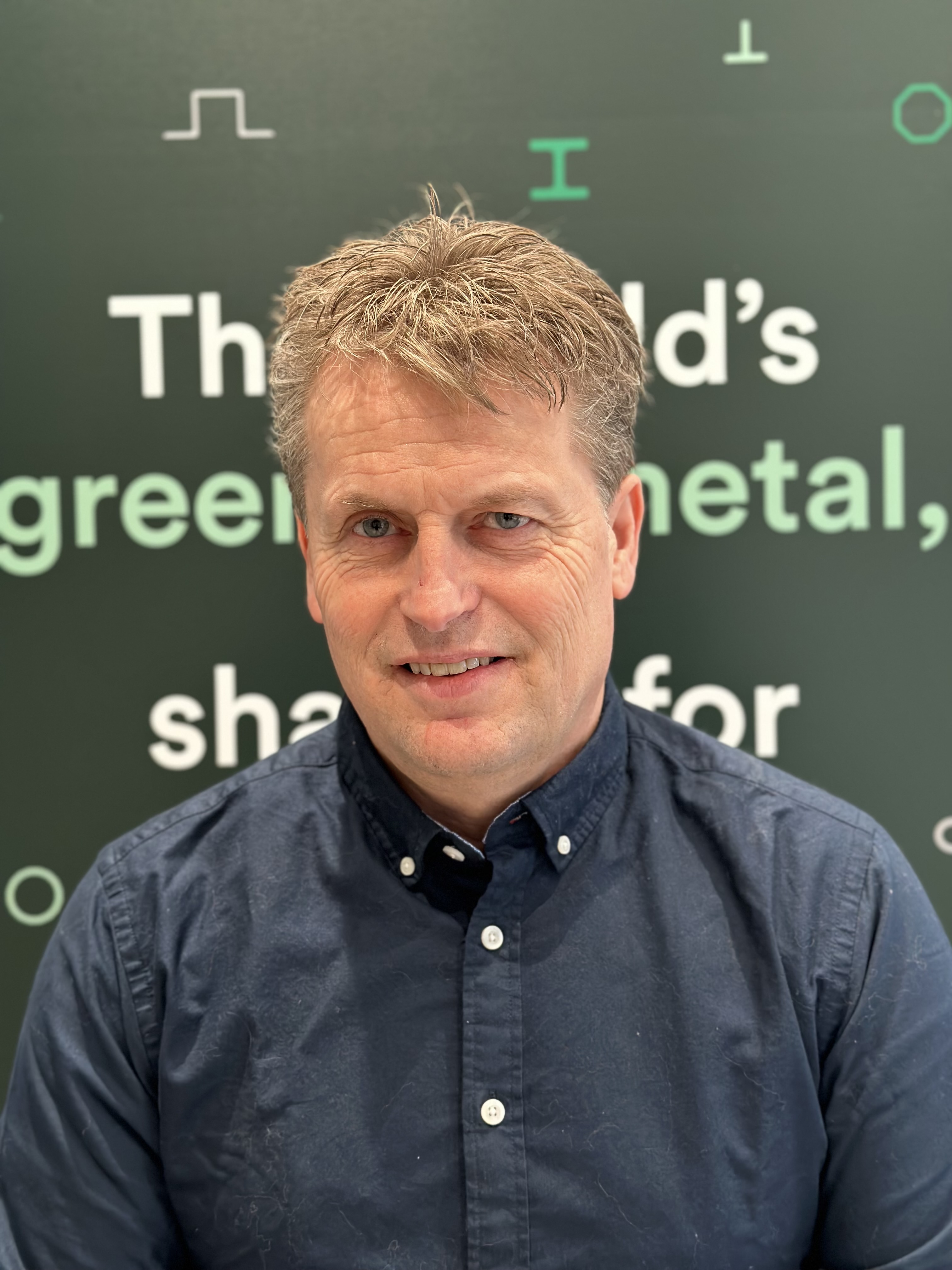
Svein Inge Nerland
Salgssjef
Our presses
We operate three different presses. Pls find detailed information about the presses below. To the right pls find information about the design capacities of each press. Actual capacities may vary depending on alloy, wall thickness, complexity and tolerances.
Raufoss Aluminum has a unique press setup enabling us to deliver on most customer needs, ranging from large demanding structures to small and light profiles.
We are offering to be your total supplier regardless of your profile requirements.
P70 (The most powerful press in the Nordics):
P22:
P12:
The extrusion process
Below you will find useful information about the extrusion process. We recommend watching the movie, as it provides a good overview of the process.
The raw material for extruded aluminum profiles is a press billet, which is made from primary aluminum, recycled aluminum, or combinations of these. The press billet is cast in lengths of about 7 meters and is available in a variety of alloys and dimensions, tailored to the specific requirements and needs. At Raufoss Aluminum, the press billet has a diameter of 152-305 mm and is precision sawed into usable lengths of 200 - 1500 mm, adapted to the extrusion press and the final profile's length.
Extrusion involves the pre-heated aluminum billet (500°C) being pressed through a profile tool under high pressure (1200-7000 tons depending on the press size). The tool's opening corresponds to the profile's cross-section. The extrusion speed depends on the alloy and the profile's complexity, but typical speeds range between 5 and 100 m/min.
As the extruded profile exits the tool, it is led out onto an exit and cooling table where it is cooled by air or water, depending on the profile's size, shape, alloy, and desired properties. To ensure the profiles are straight and to relieve any stresses in the material, the profiles are stretched.
Thereafter, the profiles are cut to suitable lengths and sent for age hardening. Hardening takes place in an oven at typically 5 hours at a temperature of about 200°C. Finally, a final inspection is conducted, and the profiles are ready for further processing or shipment to the customer.
Our factory
Did you know that our factory is as long as the Eiffel Tower, and that we have both anodizing and painting facilities next door ? Read more about our factory below.
All based and produced in accordance with IATF16949 quality standard.
Picture of our factory